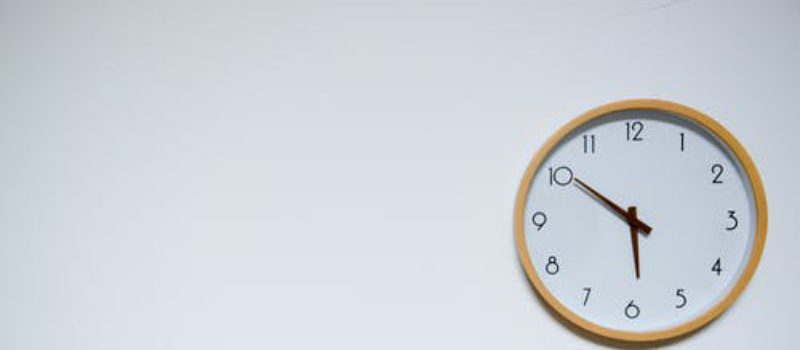
Every time your business receives an order is a “moment of truth” both for your consumer’s customer experience, as well as the profitable health of your business. The clock is ticking: can you meet the customer's delivery expectation while maximizing your margin?
If you’re managing your Digital Ecosystem properly, there should be no doubt that the product ordered is actually in stock within your internal facilities or wider external inventory network. If this is often not the case, you and I should have a different conversation on how to quickly and easily fix that problem!
Increasingly, in order to meet faster delivery timelines and reduce transport costs, many brands and sellers are now opening multiple delivery locations, and as soon as you open more than one fulfillment location option, you will need some form of Distributed Order Management (or DOM for short) to determine from which location it’s best to ship.
We simply define DOM as:
Distributed Order Management (DOM) – A networked inventory and order management system which selects and routes orders to the optimal fulfillment location based on an automated, rules-based decision process without the need for user intervention.
In the end, it really doesn’t matter what slick network design and software modeling tools you’ve used to design your network, or even what additional product is currently on the way to your warehouse. What really matters right now is what happens in that moment in time when that consumer places an order on your website, via a marketplace or on a retailers site for drop shipping, as it’s now decision time!
This can run from the very basic of, we have two warehouse fulfillment centers and only one has the needed product in stock, so it’s quite easy to decide to ship from that warehouse!
But what if the product is available in both warehouses, which do you choose? The answer here requires an understanding and calculation of shipping cost from each location.
Add to this the complexity of multi-item orders as well as several warehouse fulfillment centers, and other external inventory options, and the decision process can quickly become very intensive.
As you can imagine, there’s numerous potential capabilities and functionalities which can be delivered through Distributed Order Management.
Some key areas to focus on to ensure you get the most bang for your DOM buck are:
1) Can the DOM hold different inventory costs for various product inventory locations, ie: if considering distributor inventory closer to consumers there may be a higher cost, but due to proximity to end consumer, total delivered cost is lower.
2) Can the DOM leverage inventory availability from other system types or does the DOM’s host system need to be installed in every location where inventory is to be considered by the DOM logic?
These two items are only the tip of the iceberg when it comes to the potential functionality and variables to be considered by advanced Distributed Order Management systems.
But for now I’ll leave you with this question, when these moments of order truth start to come by the thousands, or even tens of thousands of times a day, will you be using the most optimal and capable solution to drive the maximum profit and customer delight possible in each moment of truth?
To view this entire article from Jeff Ashcroft on LinkedIn, click here.
Additional resources
ETAIL PLATFORM OVERVIEWS
BLOG POSTS
Distributed Order Management (DOM): What It Is, Why It’s Necessary, How to Get Started
Choosing the Best Distributed Order Management System
Maximizing Customer Satisfaction with Distributed Order Management
Nine Non-Obvious Advantages Of Distributed Order Management (DOM)
Best Practices in Distributed Order Management
WHITE PAPERS
Distributed Order Management Solutions Overview
The Ultimate Guide to Order Management
VIDEOS
Distributed Logistics for Digital Commerce: Distributed Order Management (DOM)